Why Register?
- List Your Business
- Business Matchmaking
- WhatsApp Chat
- Personal Messaging
- Showcase Your Products
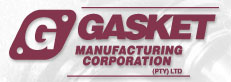
Product Pictures
New products and processes are developed with the demand for gasketing to provide a good seal under increasing pressure, temperatures and new chemicals.
Locality ensures rapid supply to all main industrial areas nation-wide and with a 24 hour operation we pride ourselves on the ability to supply on time. Assuring you of the highest standards of quality and service.
Our operations, which produce on average 3 million components, are housed under a 13 000 m2 factory, and employs a team of 150 Staff.
Our Sales Team have been extensively trained to advice on the various types of gasketing materials. With manufacturing and distribution plants in both Durban, and Cape Town, as well as a distribution point in Europe.
AUTOMOTIVE GASKETS
Automotive gasketing has developed from the early days of copper, leather and basic cork to non-asbestos, silicones and a variety of metals.
The modern engine demands high pressure sealing and must cope with differential rates of expansion and contraction between flanges. Engines are constructed from alloys with less contact area for the gasket to do its job, but with greater energy output.
CYLINDER HEAD GASKETS
The development is toward embossed or laminated metal with selective coating and also flat metal covered with gasket materials, which are in turn, enhanced with silicones. The result is a gasket which conforms to surface irregularities which can accept surface movement, can seal under arduous conditions and can be easily removed. More use is being made of new materials and enhancing the gasket with silicon coating and silicon beads adds to improved performance of the gasket.
SUMP AND VALVE COVER GASKETS
Oil pan and valve covers in pressed metal format use a variety of rubber mouldings and CorkRubber provides a good seal. On cast aluminium types, asbestos and non-asbestos materials are more applicable. (Refer to our product range and specification).
EXHAUST AND MANIFOLDS
Metal gasket composites (or metal clad jointing) allows for differential expansion rates between the manifold and engine whilst sealing exhaust gas at high temperatures.
SEALS
Range from standard NBR (Nitrile) to silicones and high temperature Viton and are sourced worldwide to suite the application.
INDUSTRIAL GASKETS
Gasket selection requires examination of three basic elements, namely:
• The medium being sealed
• Temperature and pressure influences
• The construction of the flange where the gasket will be fitted
Determining the material which can be used to the best effect, must ensure that what is being sealed will not cause gasket degradation and be able to conform to flange irregularities without physical distortions to the flange.
CORKRUBBER AND RUBBER
Used for sealing oils, air and water at low bolt loads. Service is seen in the heavy electrical industry in transformers and switchgear. Cork rubber has a good resistance to oil at 80-100°C and is resistant to the effects of climate. Many applications ranging from gearboxes, inspection covers to water piping gaskets use rubber or CorkRubber.
ASBESTOS / NON-ASBESTOS COMPOSITES
With the demand for ever increasing pressures and temperatures, asbestos jointing is now being replaced by non-asbestos composites and can be used for high temperatures and pressures. However both ranges of materials cover a wide spectrum of specifications and are used throughout industry.
FELT AND SPONGES
Used for dust or very low pressure sealing. Felts are sometimes impregnated with oils or wax to include lubrication properties. Sponges are used for a variety of low pressure seals/dust covers and even in cord form for ease of installation. It is also common for sponge gaskets to be supplied with a peel off self adhesive backing.
ENGINEERING PAPERS AND SHIMS
Still providing good service are the engineering papers used where high flange loads are available but low pressure is evident i.e. gear boxes. Shims in plastic are coloured to positively identify the precise thickness to allow for accurate settings.
PLASTIC SHIMS
Using colour coded shim material provides easy, reliable and fast recognition of their thickness by their colour. There is no need to use a micrometer thus saving on time and costs and providing greater dependability on assembly and improving of the quality of the finished product.
In many applications plastic shims, can replace metal due to the improved technology in providing perfomance characteristics which differ from those of metal, e.g. folding endurance, chemical resistance, tensile strength to break, etc. Plastic shims also cost less than metal which adds to their cost effectiveness.
APPLICATIONS AND INDUSTRIES
Arbor shims for milling machines; slitting machinery for steel or non-metals; pumps; power transmissions; reduction gear units; all types of filters; compressors; diesel engines; escalator and elevator manufactures; all engineering workshops; earth moving equipment; mining equipment; marine applications; optical equipment; vehicle washing equipment; dot matrix printers; bearings; nuclear power plants.
Chemical resistance to:
Acetic acid, hydrochloric acid 10%, sodium hydroxide 10%, water, tricoethlene, detergent oils 10°C, detergent oils 90°C, other hydrocarbon oils.
SIZES AND AVAILABILITY
Metric size range from 0,012 mm to 1,0 mm
Non-metric sizes range from 0,0005” to 0,04”
Available in sheets 1220 x 610 mm
Some thicknesses are available in bulk length rolls of 250metres x 0,610 wide. These materials can be cut into any shape and/or size.