Why Register?
- List Your Business
- Business Matchmaking
- WhatsApp Chat
- Personal Messaging
- Showcase Your Products
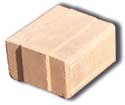
Product Pictures
We are property developers using soil-cement technology for building blocks as opposed to conventional sandcrete blocks. We work mainly in Africa but have emerging markets in Eastern Europe and Middle East.
At Hydraform, we are dedicated towards rebuilding Nigeria block by block with our very innovative Hydraform Blocks. Hydraform Blocks are top of the line in the Building Construction industry that gives a unique building system which encompasses excellent thermal properties, higher compact strength, an outstanding speed of construction, environmental friendliness and a substantial cost saving.
Hydraform building system replaces conventional bricks and mortar through the use of Hydraform blocks, which are largely dry-stacked. The other components of the conventional building system remain unchanged. The blocks are manufactured by hydraulically compressing a soil-cement mixture. Hydraform building blocks are in use throughout Nigeria as well as in South Africa, Argentina, India, numerous African countries, Mexico and the United States of America. Use is predominantly in the construction of housing, schools, walls and general single and multi-storey buildings.
Visit our offices and we will introduce you to our Machines, Products and Services, and also offer you a grand opportunity of buying beautiful housing units that are up for sale.
BLOCK PRODUCTION
A 4MPa block requires a 1:20 ratio of cement to soil. This means that for one bag of 50kg cement (+-33 liters) you will need about 10 wheelbarrows (+-65 liters/wheelbarrow) of soil. This mix yields about 75 blocks. For a 7MPa block the ratio is 1:12 cement t soil. A 50kg cement bag is mixed with 6 wheelbarrows of soil, giving you about 45 blocks.
5% cement = 1bag of cement = +- 75 blocks therefore produce
8% cement = 1 bag of cement = +-45 blocks.
Each 220mm block weighs about 11kg. From a one ton soil mixture you should therefore produce +-90 blocks.
On average 1m3 of soil will give you 105 blocks.
The average water consumption is +-1 liter of water per bock.
The diesel tank can take about 10liters of diesel. You will use about 1.5 liters of diesel per hour. 10 liters of diesel is enough to produce 1300 blocks. You will require +/- 12 liters of diesel per 1500 blocks.
A team of 7 – 8 men can produce +/- 1500 blocks per 8hr shift at full production.
SOIL TYPE
Hydraform blocks are produced with a sandy soil with clay and silt content between 10-45%. Silt and clay is the finest fraction of all soils. It is essentially the DUST within the soil. Soils with higher clay content can easily be mixed with sand. The soil often used is a Laterite soil or a Loamy soil. Depending on the soil type a water content of 8-12% is required.
BLOCK PRODUCTION PROCESS
- Find and test the soil to be used
- Move the Hydraform block making machine to the construction site
- Mix soil and cement in predetermined ratio’s by hand or in the Hydraform pan mixer
- Load the soil-cement mix into Hydraform block making machine and produce block (15-20 seconds per block)
- Stack Hydraform blocks for curing
- Cover blocks with plastic immediately and water them daily for 7 days or more.
Hydraform Building System
Hydraform has many benefits for the user including:
Substantial cost savings because freely-available subsoil is the main raw material; the blocks do not require costly burning; transport costs are minimised since block production takes place on site; unskilled labour can be trained in both blockmaking and building with Hydraform blocks.
Mortar is largely eliminatedin superstructure walls because the interlocking blocks are dry-stacked except in the ring beam and in high gables.
Speed of constructionis a valuable feature of the System, which is much faster than other building methods. A bricklayer can lay at least 800 Hydraform blocks (21 m2 of walling) per day.
Excellent thermal properties – Hydraform blocks have excellent thermal capacity (the ability to absorb and hold heat). Prof. John Morris of the Faculty of Building & Quantity Surveying at the University of the Witwatersrand, Johannesburg states: “… Hydraform blocks are three times as efficient as concrete and almost twice as efficient as fired clay bricks … in terms of the thermal insulation they offer.”
Environmental friendlinessis a major feature of the Hydraform system; blocks are produced under high compression from subsoil, without the need for the fuel-wood used to burn bricks.
High strength has been demonstrated in Hydraform structures, showing that these have considerably higher impact strength than those constructed from concrete blocks.
Attractive, face-brick finishesare achieved with Hydraform blocks in a variety of natural colours derived from the soil found at individual sites. The interior walls may be plastered, painted or sealed.
Simplicity characterises the Hydraform Building System. Both the production of blocks and the erection of walls using Hydraform blocks are simple; relatively unskilled labour may be used to carry out both processes, operating under Hydraform-trained supervision.
MACHINERY
- M7 EPU Mobile Block Making Machine
- M7 S2D/E Stationary Blockmaking Machine
- M7 Twin Mobile Blockmaking Machine
- M7 ExM Mobile Blockmaking Machine